The Comprehensive Guide to Plastic Injection Molding in China
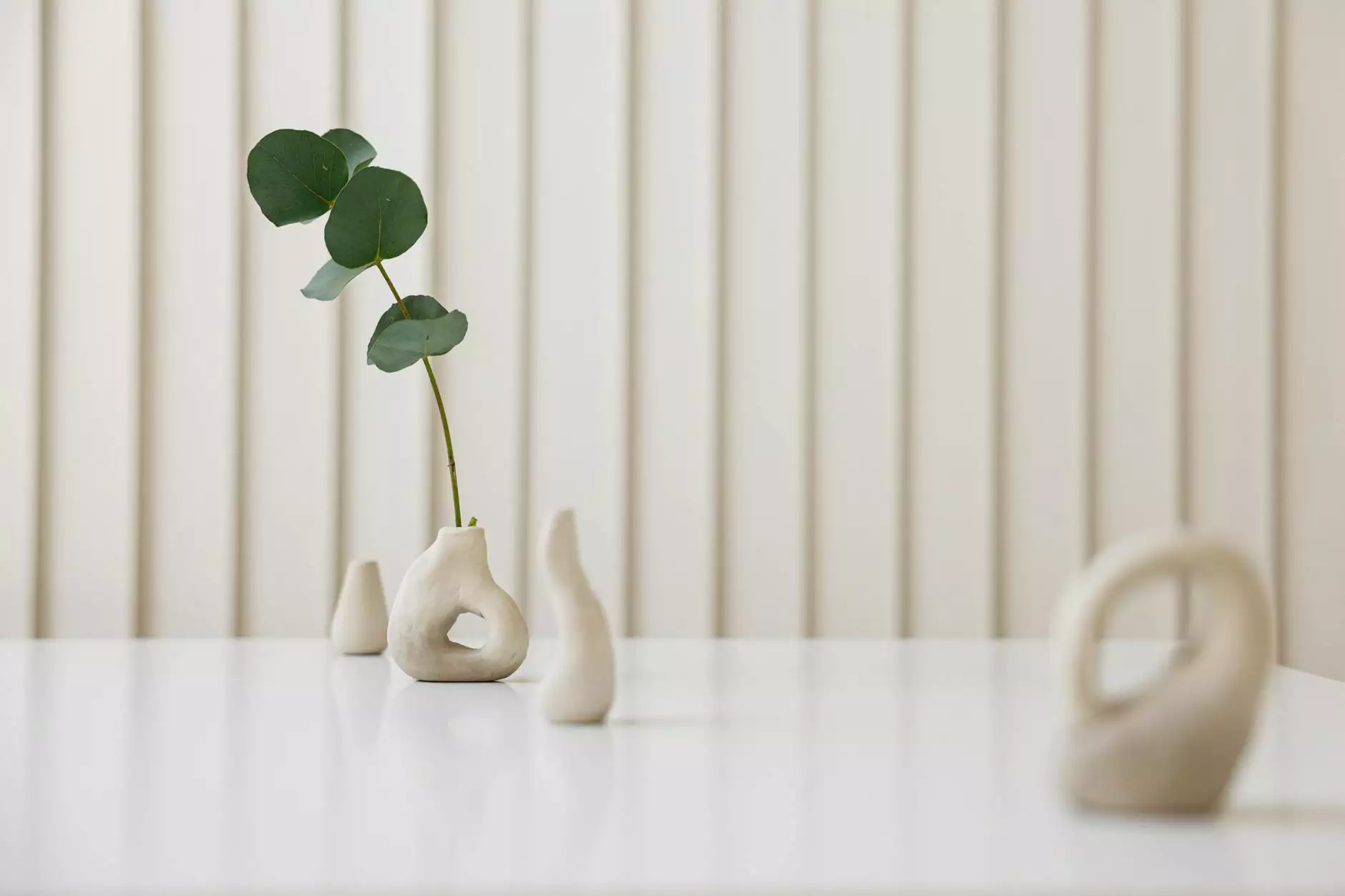
In today’s fast-paced manufacturing environment, plastic injection molding has emerged as a pivotal technique for producing high-quality plastic components efficiently. Among the leaders in this arena, China has established itself as a powerhouse, offering innovative solutions that cater to a variety of industries. In this article, we delve into the nuances of China plastic injection molding, examining its advantages, processes, and the exceptional services provided by Hanking Mould, a distinguished Plastic Mold Maker and Plastic Injection Mould Manufacturer.
Understanding Plastic Injection Molding
Plastic injection molding is a manufacturing process that involves injecting molten plastic into a specially designed mold to create various items ranging from intricate components to larger structural parts. This method is favored for its ability to produce complex shapes with high precision and minimal waste, making it incredibly efficient for mass production.
How Plastic Injection Molding Works
- Design Phase: The process begins with the design of the product and the mold. CAD (Computer-Aided Design) software is used extensively to create detailed 3D models.
- Mold Creation: Once the design is finalized, the next step is to manufacture the mold using high-quality steel or aluminum, which can withstand repeated use.
- Injection Phase: The raw plastic material, usually in pellet form, is heated until it melts and is then injected into the mold under high pressure.
- Cooling Phase: After injection, the molten plastic is allowed to cool and solidify. The time required for cooling depends on the type of plastic and the thickness of the part being produced.
- Mold Opening: Once the plastic has cooled and hardened, the mold is opened, and the final product is ejected.
- Finishing Touches: Additional processes such as trimming, painting, or assembling may follow based on the product requirements.
The Advantages of Plastic Injection Molding in China
There are numerous reasons why businesses around the globe choose to tap into China's plastic injection molding capabilities. Here are some notable advantages:
- Cost-Effectiveness: China is renowned for its competitive manufacturing costs, significantly reducing overhead compared to Western countries.
- Advanced Technology: Chinese manufacturers continuously invest in cutting-edge technology and machinery, ensuring high precision and quality.
- Skilled Workforce: The workforce in China's manufacturing sector is well-trained and experienced in various production processes, including plastic injection molding.
- Scalability: Chinese manufacturers can scale production up or down efficiently, catering to both small orders and large mass productions.
- Rapid Turnaround Times: With robust infrastructure and streamlined processes, manufacturers can often produce and deliver products faster than competitors.
Applications of Plastic Injection Molding
The applications of plastic injection molding extend to various industries. Here are some key sectors utilizing this technology:
- Automotive Industry: Injection molded parts are used for dashboards, panels, and other vehicle components.
- Consumer Electronics: Covers for devices, housings, and connectors are all commonly produced using injection molding.
- Medical Devices: Precise and sterile components like syringes, disposables, and housings for equipment.
- Household Items: Items such as storage bins, kitchen utensils, and cosmetic containers are frequently made through this process.
- Toys and Recreational Products: Plastic toys, sports equipment, and outdoor gear leverage injection molding for quality and safety.
Hanking Mould: Your Partner in Plastic Injection Molding
Hanking Mould has established itself as a leading Plastic Injection Mould Manufacturer in China, known for its commitment to quality and customer satisfaction. Here are some key features that set Hanking Mould apart:
High-Quality Manufacturing
At Hanking Mould, the focus is on quality assurance throughout the production processes. By adhering to international standards and incorporating cutting-edge technology, Hanking Mould ensures that every product meets stringent quality controls.
Custom Design Services
Understanding that each client’s needs are unique, Hanking Mould offers personalized design services to create molds tailored to specific applications. Their expert designers work closely with clients to bring ideas to life in the most cost-effective manner.
Fast Prototype Development
Hanking Mould emphasizes rapid prototyping, allowing clients to visualize and test their products before committing to mass production. This not only saves time but also helps identify any design flaws early in the process.
Comprehensive After-Sales Support
The journey does not end with delivery. Hanking Mould provides comprehensive after-sales support, ensuring any concerns or adjustments needed post-production are addressed promptly and effectively.
Future Trends in Plastic Injection Molding
As the manufacturing landscape evolves, plastic injection molding is poised for several transformative trends:
- Sustainability Practices: Increasing awareness of environmental impacts will push manufacturers to adopt more sustainable raw materials and recycle wastage effectively.
- Smart Manufacturing: Integrating IoT and AI technologies into production processes will lead to smarter manufacturing solutions that enhance efficiency and reduce costs.
- Bioplastics: The introduction of bioplastics into injection molding processes is likely to grow as industries seek more environmentally friendly alternatives.
- Increased Automation: The implementation of advanced robotics for handling post-processing will streamline operations and reduce labor costs.
Conclusion
In summary, China plastic injection molding is a vital component of modern manufacturing, offering numerous advantages that bolster the production capabilities of businesses worldwide. With leaders like Hanking Mould providing innovative solutions, high-quality manufacturing, and dedicated customer service, the future of plastic injection molding looks incredibly promising.
For businesses looking to leverage the strengths of plastic injection molding, partnering with experienced manufacturers like Hanking Mould can be the key to success. Embracing the benefits of this process can lead to reduced costs, enhanced product quality, and ultimately, a competitive edge in the marketplace.