Understanding LOLER Meaning in Business
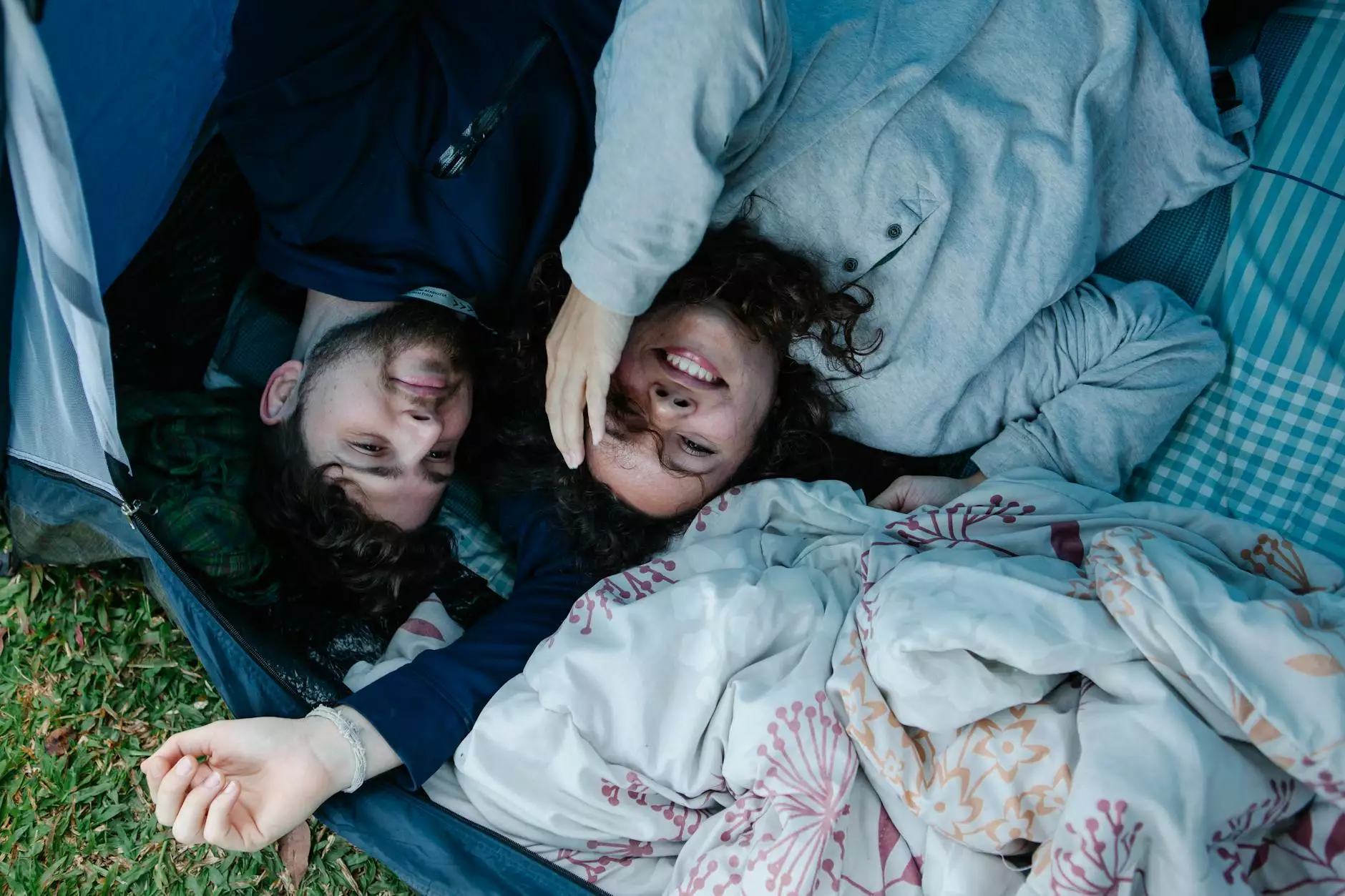
In the realm of business operations, particularly within sectors like Home & Garden, it is essential to understand various regulations and terms that can significantly impact safety and compliance. One such term that often comes up is LOLER meaning, which stands for "Lifting Operations and Lifting Equipment Regulations." These regulations are crucial for ensuring that lifting equipment is used safely and correctly.
The Fundamentals of LOLER
LOLER is part of UK health and safety legislation that aims to ensure the safe use of lifting equipment in the workplace. Established in 1998, LOLER applies across various industries, including construction, waste management, and surprisingly even in the gardening sector. As businesses, especially those involved in pest control and gardening, often use lifting equipment such as hoists, cranes, and forklifts, understanding LOLER is essential.
Key Objectives of LOLER
- Safety Assurance: Protects workers by ensuring lifting equipment is safe to use.
- Regular Inspections: Requires regular inspections and maintenance of lifting equipment.
- Proper Training: Ensures that operators are adequately trained to use the equipment.
- Documentation: Mandates record-keeping of inspections and maintenance activities.
Why Every Business Should Be Aware of LOLER
In businesses that utilize lifting equipment, compliance with LOLER is not just a recommendation—it is a legal requirement. Understanding the loler meaning is vital for several reasons:
Legal Compliance
Failing to comply with LOLER can result in severe penalties including fines and even imprisonment for gross negligence. For business owners in the Home & Garden sector, such as gardeners who might use cranes for tree removal or pest control services needing lifting equipment, understanding and adhering to these regulations is non-negotiable.
Employee Safety
Workplace safety should always be a top priority. By adhering to LOLER regulations, businesses can actively reduce the risk of accidents related to lifting operations, ensuring that their employees remain safe while carrying out their duties.
Improving Operational Efficiency
Businesses that follow LOLER not only comply with legal standards but also tend to experience fewer accidents. This results in higher operational efficiency. When lifting equipment is regularly inspected and maintained, it operates more smoothly, hence enhancing productivity.
Understanding Key Components of LOLER
The LOLER regulations provide a framework that businesses must adhere to, and understanding these components is essential for successful implementation:
1. Lifting Equipment Definitions
LOLER defines lifting equipment as any equipment for lifting or lowering loads. This includes:
- Hoists
- Cranes
- Forklifts
- Elevators
- Scissors lifts
2. Risk Assessment
Every business must conduct a risk assessment on their lifting operations. This involves:
- Identifying potential hazards associated with lifting equipment.
- Evaluating the risks and determining appropriate control measures.
3. Training Requirements
Employees must be properly trained to operate lifting equipment. LOLER mandates that:
- Operators receive adequate training and are competent in lifting operations.
- Training should be documented to provide proof of compliance.
4. Maintenance and Inspection
Regular maintenance and inspections are crucial under LOLER. Key points include:
- Any lifting equipment must be thoroughly examined at regular intervals, typically every six months.
- Results of these inspections must be recorded in a safety log.
Case Studies: LOLER in the Home & Garden Sector
Let's explore how LOLER plays a critical role in businesses in the Home & Garden sector, showcasing its relevance through practical examples.
Case Study 1: Gardeners Utilizing Lifting Equipment
Consider a gardening service that regularly handles heavy equipment like tree stump grinders and chippers. By complying with LOLER:
- They ensure that all lifting devices are safe for operation, minimizing the risk of failures.
- Regular maintenance checks help identify and resolve potential issues before they lead to accidents.
Case Study 2: Pest Control Services
In the pest control industry, vehicles equipped with lifts are often utilized to access high areas for treatment. Following LOLER ensures:
- That equipment such as aerial lifts and cherry pickers are inspected, reducing the chance of operational mishaps.
- Employees are trained on the proper use, further enhancing safety and efficiency.
Potential Consequences of Ignoring LOLER
For businesses that overlook the implications of LOLER, the consequences can be dire.
1. Legal Ramifications
Non-compliance can result in hefty fines and legal actions against the business owner and responsible personnel.
2. Increased Risks and Liability
By neglecting safety standards, businesses expose themselves to potential accidents, leading to injuries and liabilities that can cripple operations.
3. Negative Impact on Reputation
A reputation for safety and reliability is critical to a business’s success. Neglecting LOLER compliance can tarnish a brand's image, leading to loss of customers.
Conclusion: Embracing LOLER for Business Success
Understanding the loler meaning and implementing its regulations is essential for any business involved in lifting operations, particularly in the Home & Garden sector. Compliance not only ensures employee safety but also enhances operational efficiency and protects the business from legal repercussions. By prioritizing LOLER, businesses can foster a culture of safety, thrive in their respective markets, and ultimately serve their customers better.
In summary, whether you’re a gardener, involved in pest control, or operate any kind of lifting equipment, embracing the principles of LOLER is not just about compliance; it’s about committing to the safety and well-being of your workers, customers, and the integrity of your business.